The Importance of Quality Control in Structural Fasteners
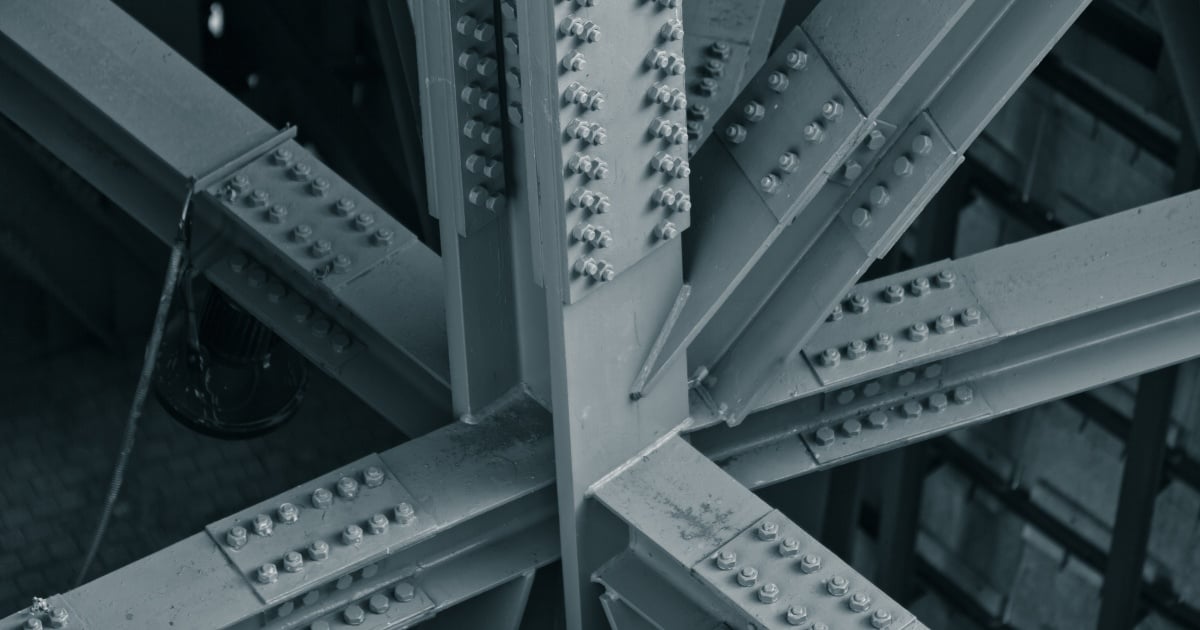
When was the last time you saw structural fasteners top a list of materials needed to start a project? Fasteners like bolts, nuts and screws often are an afterthought.
As long as it fits, the cash-strapped project manager might say, “A hex bolt is a hex bolt. Just order enough of the right size and move on.”
But the truth is the quality of structural fasteners is an essential part of every structure and product you build.
And not all structural fasteners are created equal. Quality control in these products is essential for your project’s safety, compliance and cost-efficiency.
This post walks you through three critical areas – the importance of using quality fasteners, testing products to ensure they meet all standards and the benefits of strong quality assurance.
Why Quality Control Matters in Fasteners
Fasteners are essential parts to structural integrity and safety. A defective bolt or screw can lead to catastrophic failures, such as these three examples:
1. San Francisco Bay Bridge Bolt Failure: In 2013, an analysis revealed inferior quality in seismic safety bolts. Crews replaced hundreds of critical support bolts. Although no one died, bolt replacement cost an estimated $45 million.
2. Minneapolis I-35W Bridge Collapse: In 2007, corrosion and material fatigue led to disaster – 13 people died and 145 were injured.
3. Tacoma Narrows Bridge Collapse: In 1940, a catastrophic failure of this suspension bridge in Washington state resulted from critical engineering flaws, including poor structural design and inadequate fastening mechanisms.
Tests for Structural Fastener Quality Control
Trusted manufacturers run their products through a series of quality assurance measures. Lab/testing services evaluate products for:
- Material integrity: Manufacturers test metallurgical and chemical composition to make sure materials meet industry standards, like ASTM F3125 and ASME B18.2.6.
- Dimensional precision: This speaks to how well fasteners fit into the structure. Manufacturers use micrometers, calipers, coordinate measuring machines (CMMs) and statistical process control (SPC). Teams also conduct random sampling and critical dimension checks.
- Mechanical performance: Tests for tensile strength, proof load capacity and hardness all ensure fasteners are up to code.
- Surface treatment verification: These measures assess protective coatings. Tests for corrosion resistance, salt spray/environmental exposure resistance and surface finish all ensure structural integrity.
- Traceability and documentation: Detailed record keeping also plays a vital role in quality assurance. These include lot traceability systems, manufacturing records, quality certifications (ISO 9001) and third-party quality audits.
The Benefits of Rigorous Quality Control
Well-tested fasteners are less likely to fail, ensuring safety while making sure your project meets legal standards and avoids regulatory fines. Testing also saves money in the long run, as early detection and removal of faulty fasteners reduces waste, remediation and long-term liability.
Ultimately, quality control testing pays off in customer trust, loyalty and satisfaction. Consider safety, compliance, efficiency and customer satisfaction, as these elements combine to lay a rock-solid foundation of reliability and ongoing success.
Don’t take chances on quality – work with a partner that has an ISO-certified fastener testing lab on site to guarantee products meet all standards. Contact our team to find the right fastener solutions for your business.
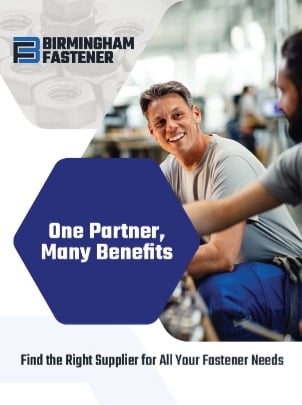
The Power of Finding the Right Partner
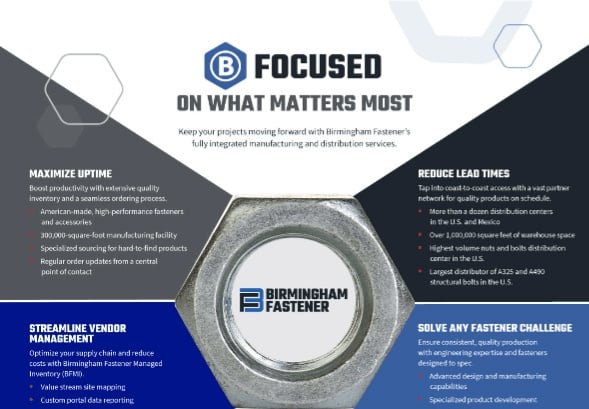
Focus on What
Matters Most
Related Posts
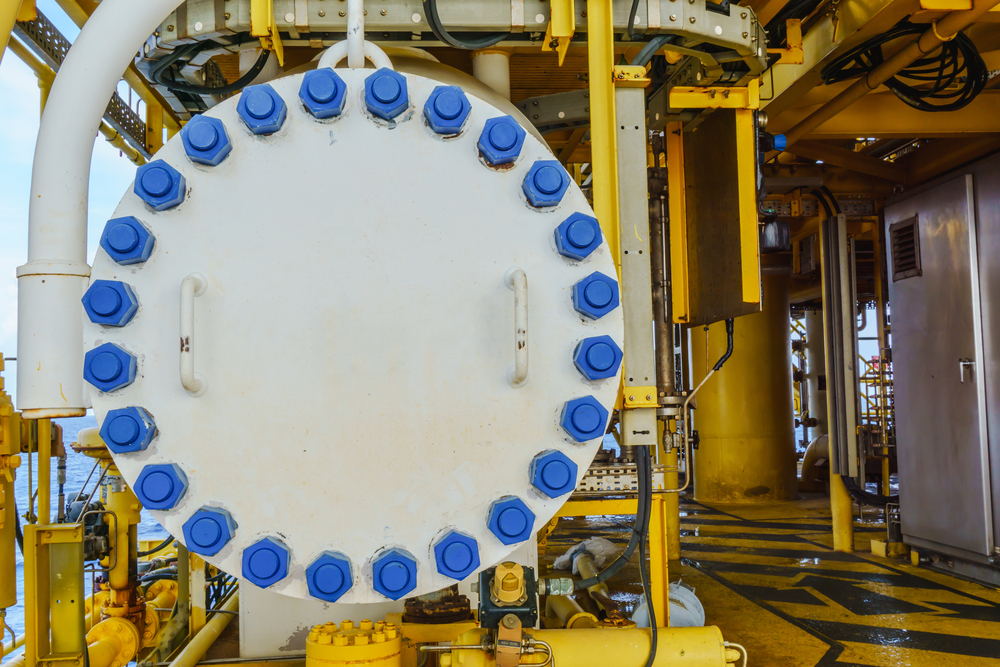
ASTM A193 B7 Stud Weight Chart | Blog
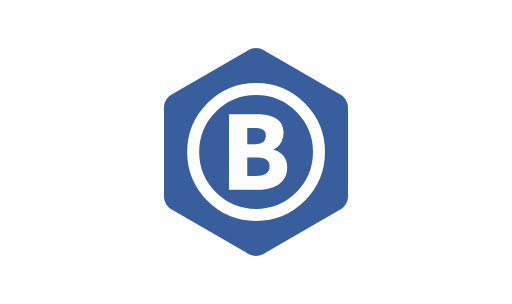
Mechanical Joint T-Head Bolt Technical Information
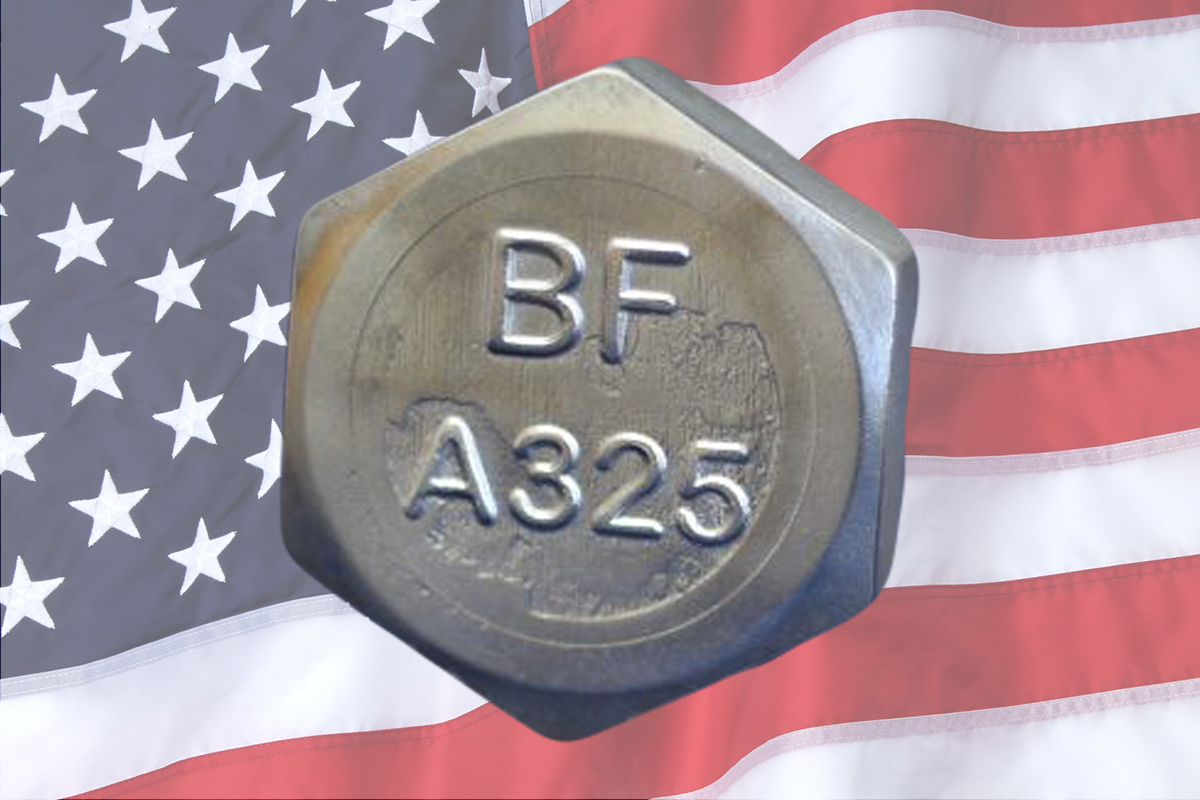