Advantages and Disadvantages of PTFE-Coated Bolts
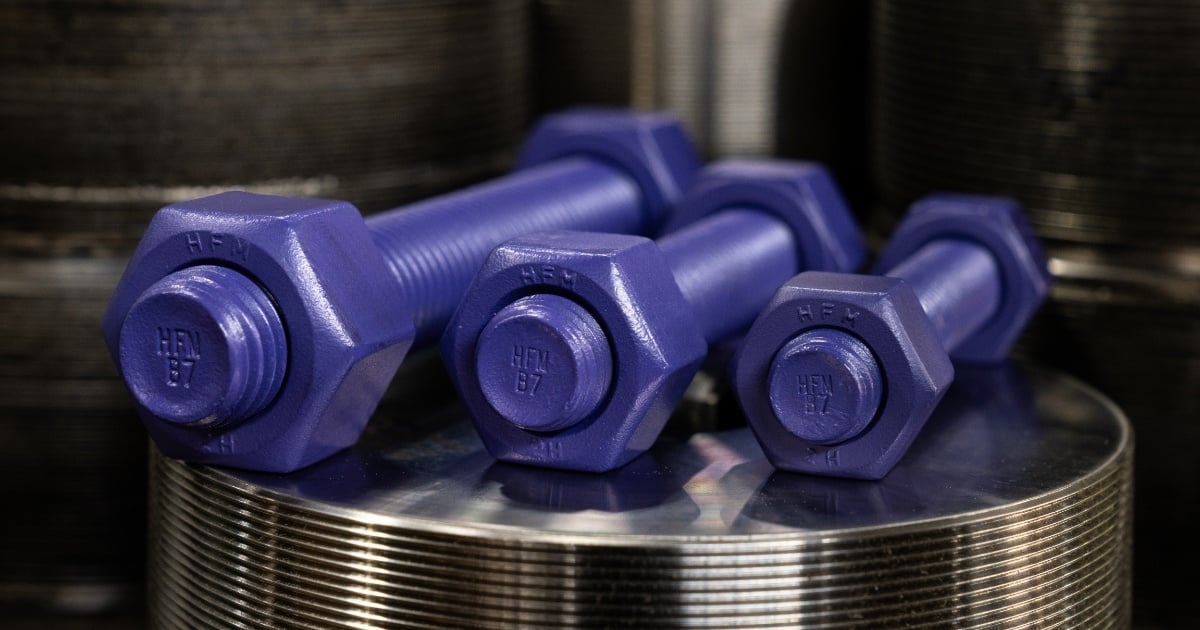
We’ve all heard about the “Teflon” coating on the nonstick pans in our kitchens, but did you know you could put it on threaded rods?
The technical explanation for Teflon is as follows:
“Polytetrafluoroethylene (PTFE) is a synthetic fluoropolymer of tetrafluoroethylene and has numerous applications because it is chemically inert. The commonly known brand name of PTFE-based composition is Teflon by Chemours, a spin-off from DuPont, which originally discovered the compound in 1938. Polytetrafluoroethylene is a fluorocarbon solid, as it is a high-molecular-weight polymer consisting wholly of carbon and fluorine.” – Wikipedia
However, the bolted flange industry typically calls this coating a Teflon or Xylon fastener.
Before PTFE-coated bolts, the petrochemical industry used other methods of making corrosion-resistant bolting components. Some were good for high temperatures, others were better at corrosion resistance, but some flange joints need the PTFE coating for chemical resistance.
Now, most of the industry uses Xylan coatings mainly for corrosion and chemical resistance. We’ll discuss some more advantages later in this article.
What Is Xylan? And Why Xylan?
Xylan is a PTFE coating and the registered name of Whitford Worldwide Company (acquired by PPG in 2019).
Xylan is the most common PTFE coating in the marketplace. The most common brand is what’s typically referred to as Xylan 1424.
They offer a whole series of Xylan coatings, but Xylan 1424 is the workhorse. That’s why we use it for our PROTINN fasteners.
When you combine our ISO 9001 manufacturing process with Xylan 1424, we can guarantee the best PTFE-coated fasteners in the industry.
Examples of PTFE-Coated Fasteners
PTFE or Xylan coating is applied to a variety of fasteners, including:
- ASTM A193 Grade B7 stud bolts
- ASTM A193 hex bolts
- ASTM A193 head cap screws
- ASTM A194 2H hex nuts
- Custom hex head applications
- Flat head fasteners
- High alloy steel
- Stainless steel bolting
- F-436 flat washers
While industry documents (e.g., ASME PCC-1) do not provide guidance on the advantages or disadvantages of PTFE-coated fasteners, our technical team for PROTINN® has done the homework for you.
Advantages of PTFE-Coated Fasteners
One of the most recognized benefits of the PROTINN fastener is its low coefficient of friction without using lubrication.
Non-coated ASTM A193 B7 stud bolts need lubrication (typically a molybdenum or nickel lubrication).
PROTINN has figured out how to achieve the correct tensile strength in your fastener without lubrication as well.
We know and have tested the difference between k-factors, not only on our products but also on our competitors.
This is how we can not only guarantee a low but also a consistent k-factor.
Disadvantages of PTFE-Coated Fasteners
Most manufacturers do not have a quality program for making PTFE-coated fasteners. They just throw on the coating and over-tap the nuts.
We have also seen PTFE-coated fasteners from foreign countries that take quality as seriously as PROTINN.
Inferior products show a k-factor ranging from 0.08 to 0.26. ASME PCC-1 states that torque is ~30% accurate. Without knowing what your manufacturer is doing, your torque can be off by 300%!
PROTINN B7 studs have a k-factor of 0.12 with 10% scatter. That’s the best in the industry, and that is what we want to deliver to our customers.
Get to know the new stud standard – see how PROTINN delivers 3-4 better torque loads than other B7 studs.
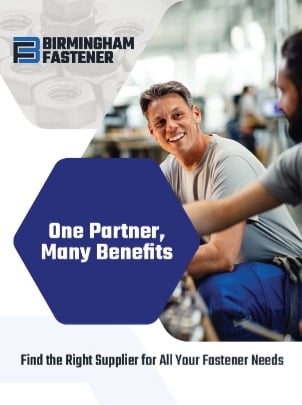
The Power of Finding the Right Partner
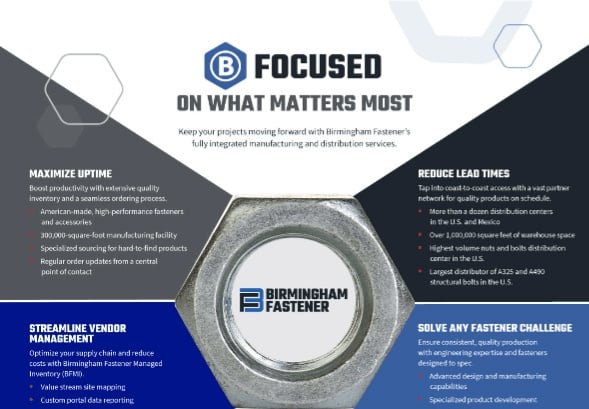
Focus on What
Matters Most
Related Posts
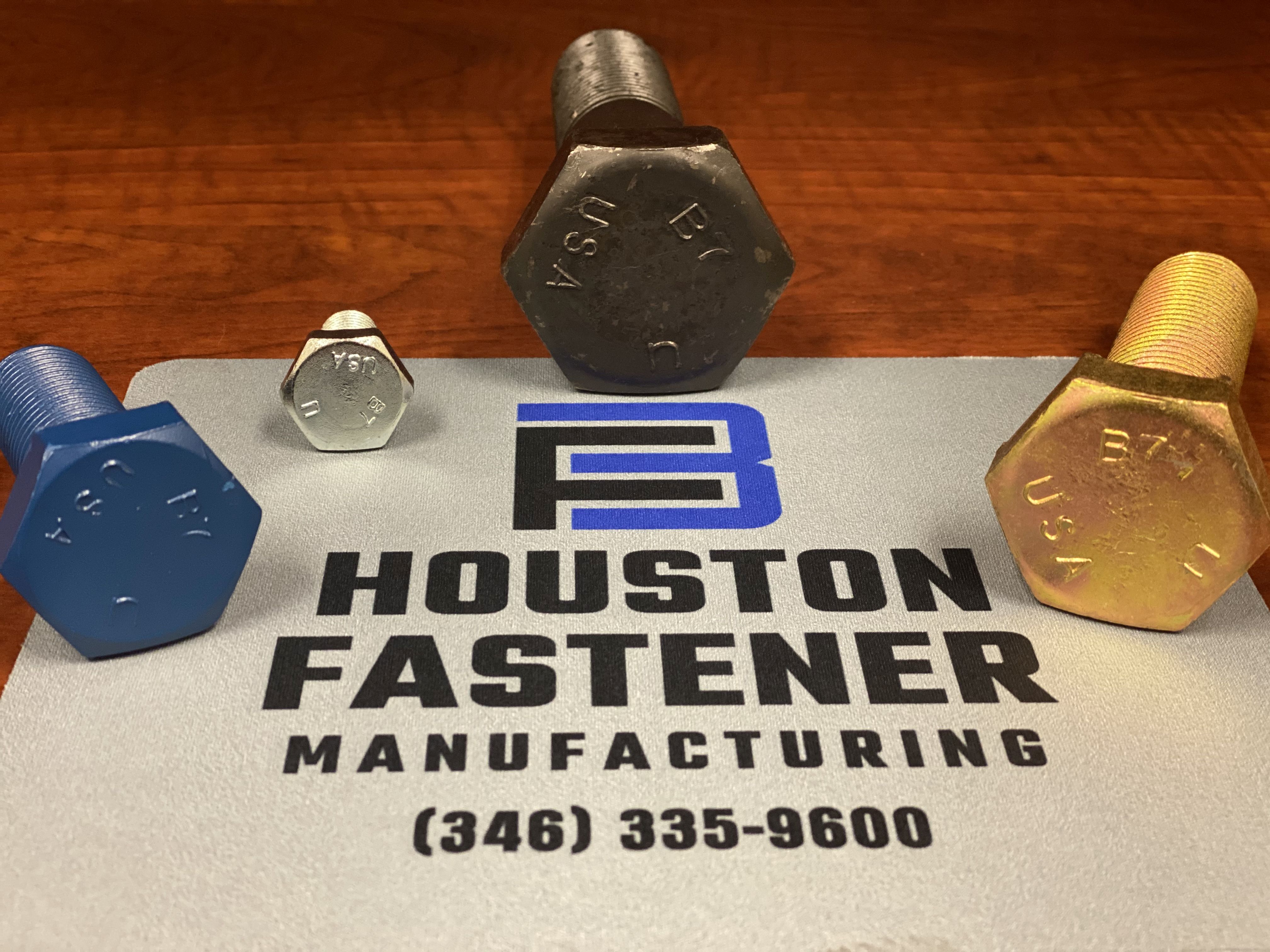
Houston Fastener Manufacturing: Serving the Oil and Gas Industry
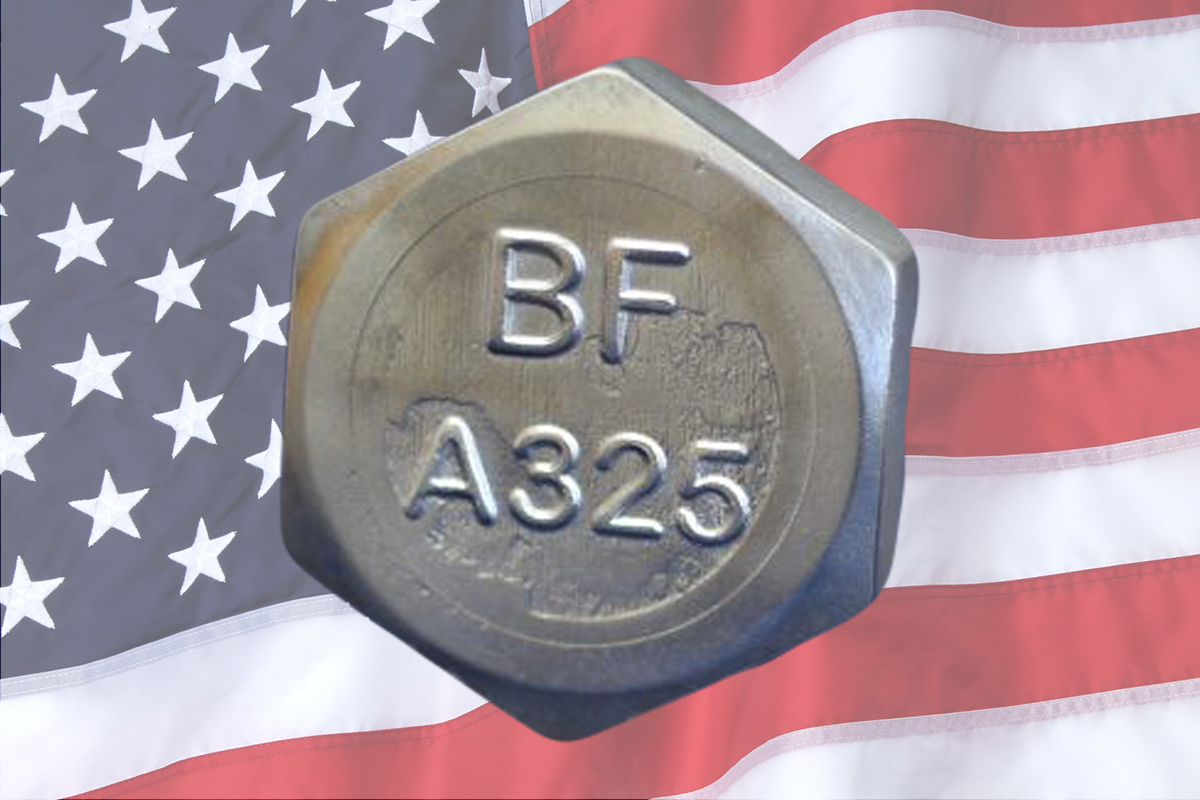