The Electroplating Process and its Benefits for Fasteners
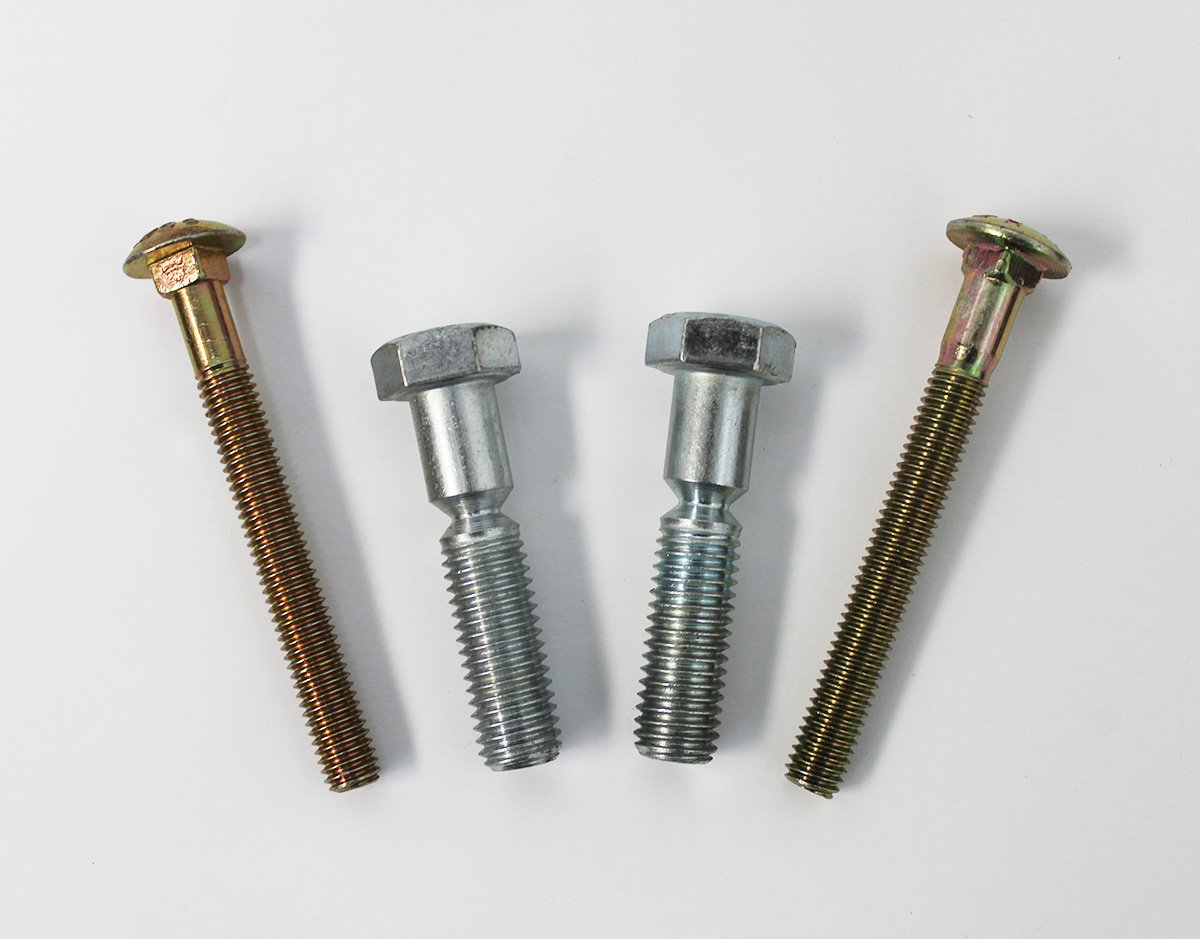
We’ve discussed a few different types of zinc coatings for corrosion resistance in the past. The electroplating process is another way to coat fasteners to ensure corrosion resistance and improve the finish of the bolt. Electroplating, or electrodepositing, is covered in the ASTM standards F1941 and B633. Let’s go over the electroplating process, characteristics of an electroplated fastener, and the benefits of this type of coating.
The Electroplating Process
To begin the process, workers clean the fastener with alkaline detergent solutions before being treated with acid. This removes any rust, oils, or other impurities on the surface of the fastener. Once cleaned, the electroplating process begins through electro deposition, or submerging the fasteners into a zinc bath. There, the direct current is sent through the chemical bath, creating a chemical reaction on the fastener, thus electroplating it.
Types of Plating Processes
Most commonly, fasteners are rack plated or barrel plated. Each have advantages and disadvantages.
In rack plating, the fasteners are left to dry on a rack after the chemical bath. This allows the threads of the fastener to remain untouched, but because the fasteners are set on a rack, the fastener ends up without the coating in certain, small areas.
In barrel plating, the fasteners are dried in a turning barrel. While you get full coverage of the coating, there runs a risk of nicked threads. If the fasteners are made from steel and then heat treated to a hardness above 39 HRC, they are baked to minimize the risk of hydrogen embrittlement. Once this process is complete, the fasteners are tested for coating thickness, corrosion resistance, and embrittlement.
Electroplating Characteristics and Benefits
Electroplating allows for a thinner coating with a clean finish, particularly compared to the hot dipped galvanized fasteners where the coating is much thicker and requires overtapping of the nut. Electroplated fasteners are typically plated in yellow or clear zinc. The yellow zinc produces a yellow/muted gold finish, while the clear zinc produces a bright, silver finish on the bolt. The benefits are mostly aesthetic, as this finish is smooth and even while still providing corrosion resistance. It is also less expensive than some other types of coatings.
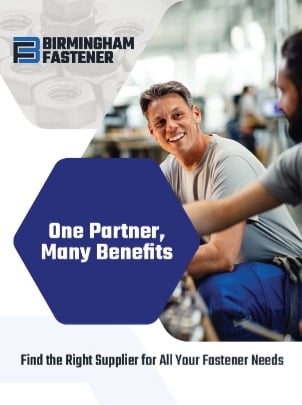
The Power of Finding the Right Partner
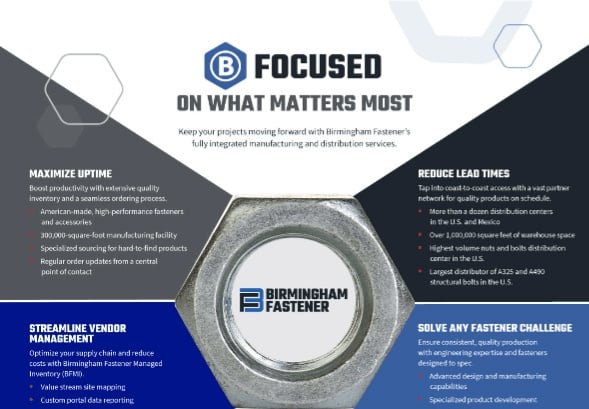
Focus on What
Matters Most
Related Posts
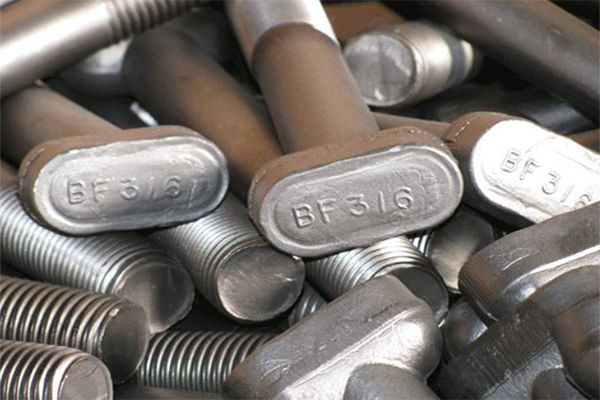
Type 304 and Type 316 Stainless Steel Fasteners
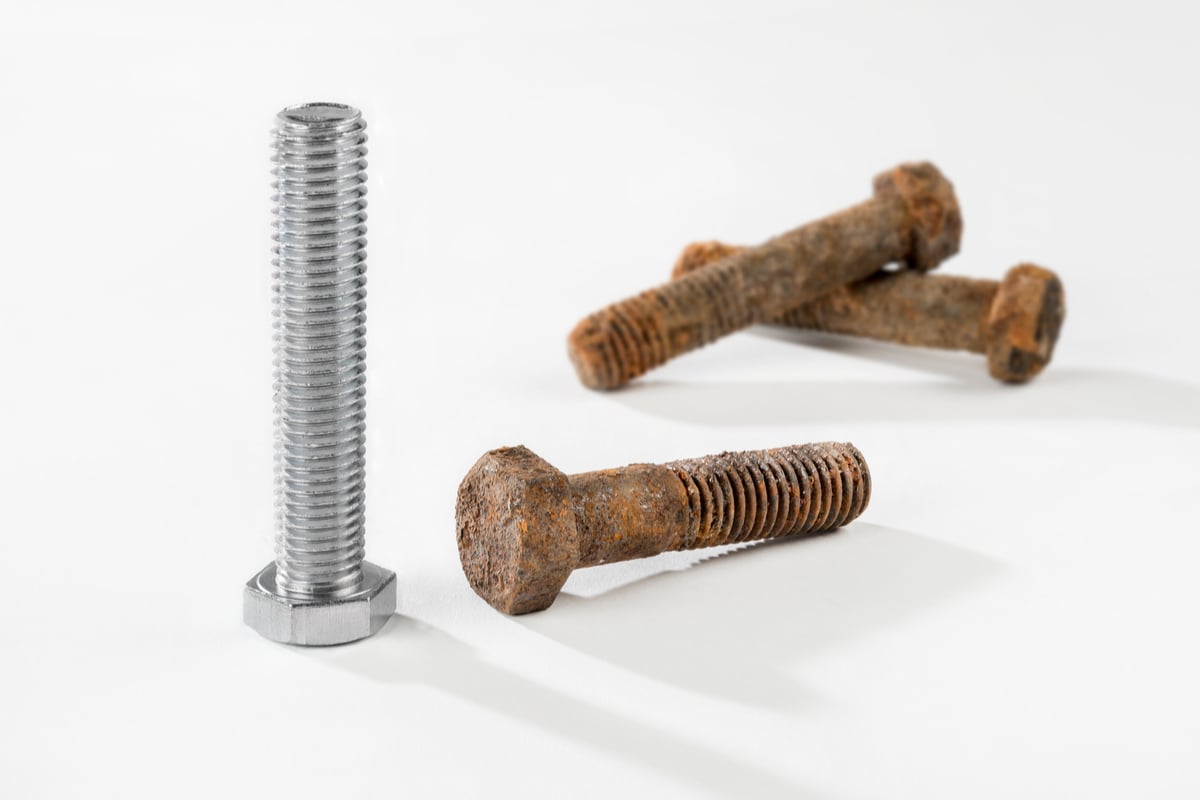
Understanding and Preventing Fastener Corrosion
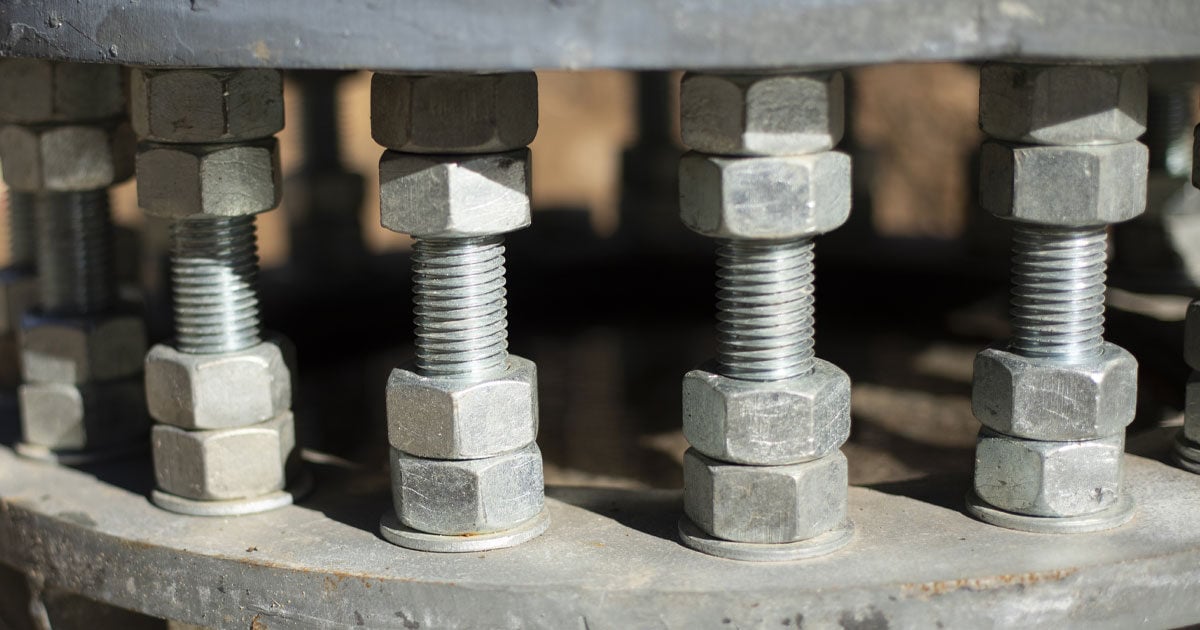