Structural Bolt Coatings
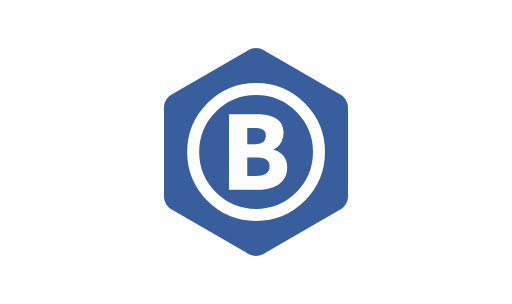
Coating structural bolting assemblies can protect the steel and ensure durability of the bolt, nut, and/or washer. There are a multiple types of structural bolt coatings, and we will touch on a few here, focusing on their characteristics, advantages, and things to keep in mind when choosing a coating. The two most common types of structural bolt coatings for F3125 Grade A325 bolts are hot-dip galvanized and mechanical galvanized. F3125 Grade A490 bolts can be coated in a zinc/aluminum corrosion protective coating or a zinc-rich base coat and aluminum coating. Zinc is used to coat structural bolts, because this metal is more reactive than iron. This ensures that the zinc coating will corrode first, thus protecting the steel fastener underneath it.
Hot-Dip Galvanizing F3125 Grade A325 Fasteners
Hot-dip galvanizing involves submerging a fastener into molten zinc to coat it. This coating is very thick, and there is a strong bond between the zinc and steel. Sometimes, the finished product will look slightly uneven compared to mechanically galvanized parts, because of the thickness of the coating. That said, hot-dip galvanized coating has more zinc per unit volume than mechanical galvanized parts, making it marginally more corrosion resistant. Hot-dip galvanizing is also generally less expensive than other types of coating.
It’s important to note that because of the thicker coating, more friction is caused when installing a hot-dip galvanized bolt than other bolts. Therefore, a rotational capacity (ROCAP) test is required for hot-dip galvanized bolts.
Mechanical Galvanizing F3125 Grade A325 Fasteners
The alternative to hot-dip galvanizing is mechanical galvanizing. This method provides a much cleaner, neater finish. The threads are smoother, and the bolt is easier to install. Mechanical galvanizing is a cold process, where the fasteners are placed in a rotary barrel that allows for a uniform coating. Though mechanical galvanizing produces a cleaner fastener, the protective coating is slightly less corrosion resistant than hot-dip, due to a weaker bond between the steel and the zinc. That said, mechanical galvanizing is a great way to ensure your bolts have a clean finish and are easy to install.
Coatings for F3125 Grade A490 Fasteners
Due to the risk of hydrogen embrittlement, A490 bolts cannot be galvanized like A325 bolts. Instead, a zinc/aluminum corrosion protective coating or a zinc-rich base coat and aluminum coating must be used. Common brands of these coatings include Geomet® and Magni®. The coating is sprayed on or dip spun, and it has a strong corrosion resistance. This coating reduces the risk of hydrogen embrittlement on the bolt.
Bottom Line
No matter what type you use, coating fasteners with a zinc barrier can help protect them from corrosion. While mechanical galvanizing produces a cleaner bolt with smooth threads, hot-dip galvanizing yields a stronger coating. F3125 Grade A490 fasteners cannot be galvanized due to the possibility of hydrogen embrittlement, but there are other great options for zinc-based coating to protect them.
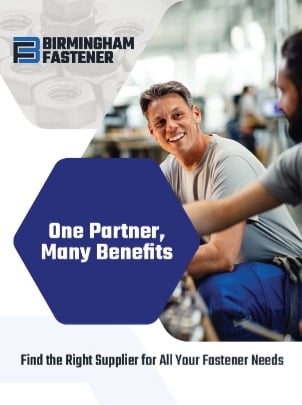
The Power of Finding the Right Partner
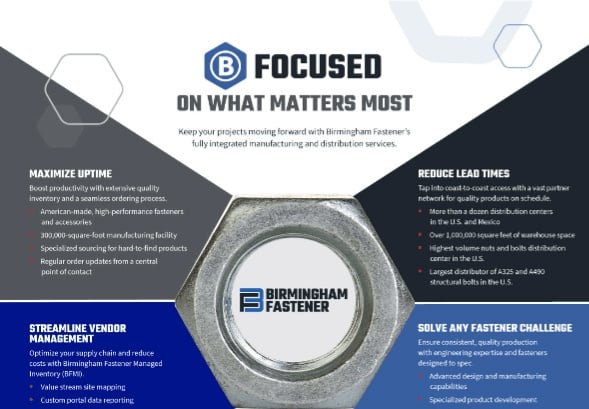
Focus on What
Matters Most
Related Posts
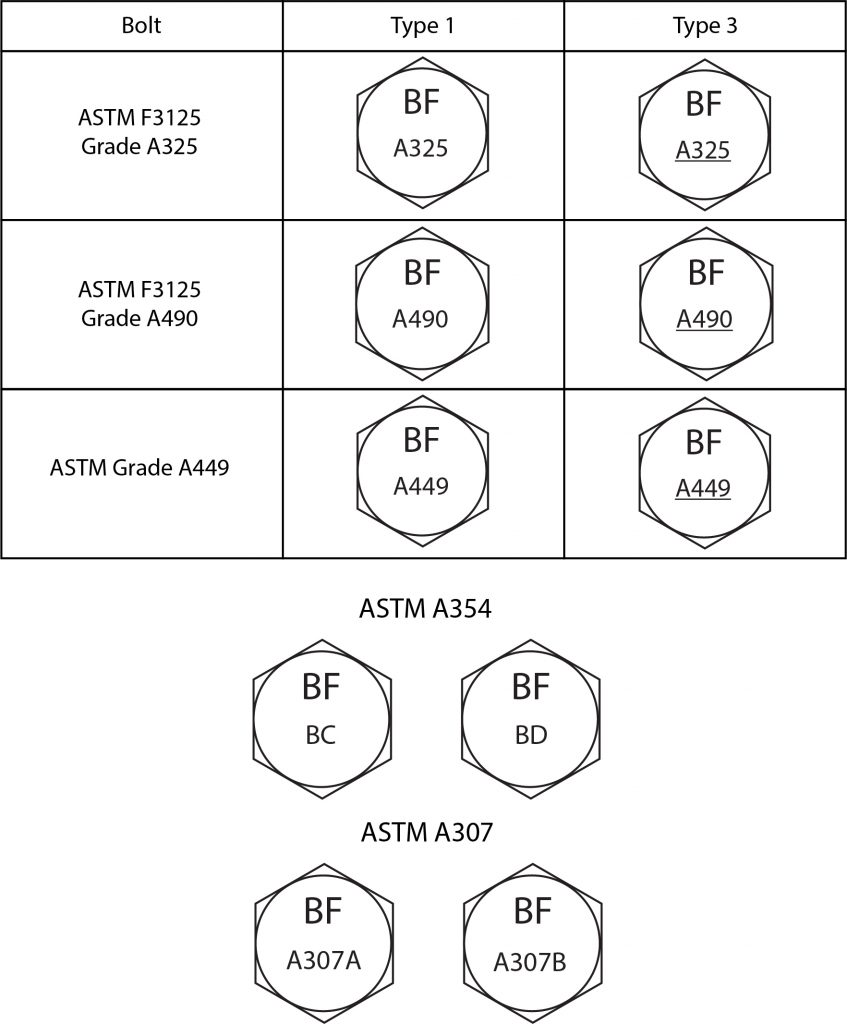
Structural Bolt Head Markings
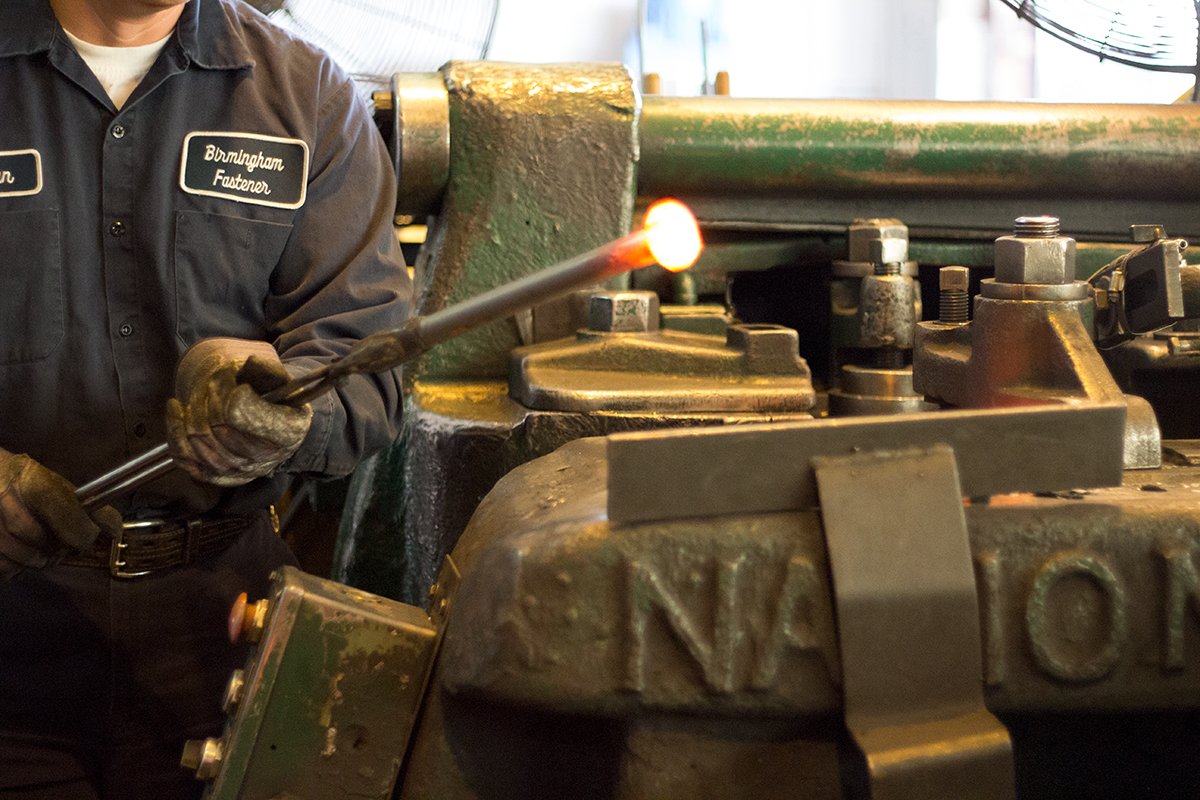
Hot Heading vs. Cold Heading – What’s the Difference?
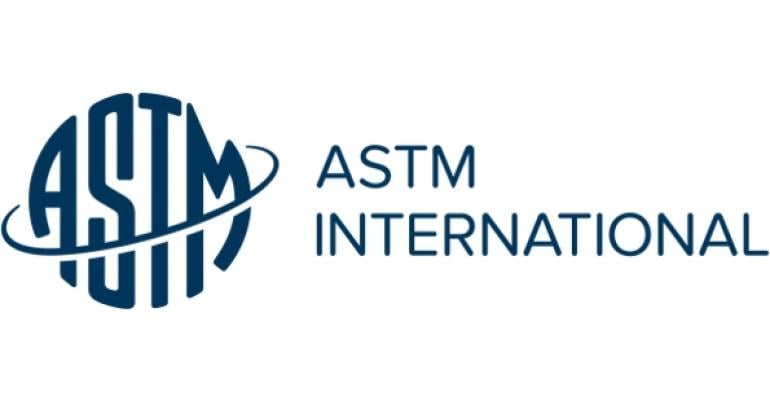